2- Stockage, mélangeage et moulage des matières premières
Ligne de production de bloc béton cellulaire avec capacité annuelle de 150 000 m3
Description de capacité:
-
Matière première principale: Sable de silice
-
Taille de la machine de coupe: 4.2 mètres
-
Taille de Moule nette (après la coupe): 4,2 x 1,2 x 0,6 m
-
Autoclave: Φ 2 x 31,5 m, 6 unités
-
Quantité de moule 26 pièces, chariot à vapeur 63 pièces, palettes de moule 152 pièces
-
Chaudière: 6 Ton / heure, 16 bar de pression.
-
Terrain nécessaire: Usine entière est 20 000 m2, Atelier est environ 6000 m2 Consommation de l’eau: 250 tonnes / jour
-
Consommation de gaz: 6250 m3 / jour
-
Consommation d’électricité: environ 6000 kW / jour
Afin d’obtenir 150 000 m3 AAC bloc par an, dans un délai de 300 jours de travail par an, nous devrions produire 500 m3 AAC bloc par jour.
Par taille du moule 4,2 x 1,2 x 0,6 = 3 m3, pour obtenir 500 m3 par jour, on doit verser et couper par jour 500 m3 ÷ 3 m3 = 167 moules.
Le temps total de travail devrait être dans les 22 heures par jour (sauf section autoclave).
Bâtiment d’usine
Le bâtiment nécessaire pour l’usine de béton cellulaire et comme suivant:
Longueur: 140 m, Largeur: 46 m, Hauteur: 9 m
Surface construite: 140 m x 46 m = 6440 m²
On peut partager la largeur en deux parties pour faciliter la construction: 46 m : 2 = 23 m
Matières premières
La formule finale sera conçue par les ingénieurs de Fournisseur selon le matériel de client
Par exemple le bloc de 550 kg/m3 AAC, nous avons besoin de la liste de matière première comme suite (juste pour la référence)
Matières premières et ses exigences
Les exigences indiquées quant aux matières premières correspondent à des valeurs idéales. Même si les matières premières divergent de ces valeurs, il est tout de même possible de fabriquer du béton cellulaire de bonne qualité. Les données définitives, le plan et les éventuelles machines supplémentaires doivent faire l’objet de clarifications au cas par cas.
Ciment: La force du produit AAC cendres volantes dépend principalement de ciment qui fournit les matériaux de calcium.
Le ciment convenable pour la production d’AAC dépend de son type.
Ordinaire ciment Portland 42,5 devrait être le premier choix.
Chaux: L’une des principales matières premières de l’AAC; l’effet principal est de fournir efficacement l’oxyde de calcium avec la coopération de la fabrication de ciment oxyde de calcium, réagir avec SiO2, Al2O3 dans l’eau chaude, puis à produire du silicate de calcium hydraté.
Par conséquent, la chaux est aussi la principale ressource de la force. L’oxyde de calcium efficace de chaux ne doit pas être moins de 65%, plus de 80% est parfait et doit être conforme aux JC / T621-1996.
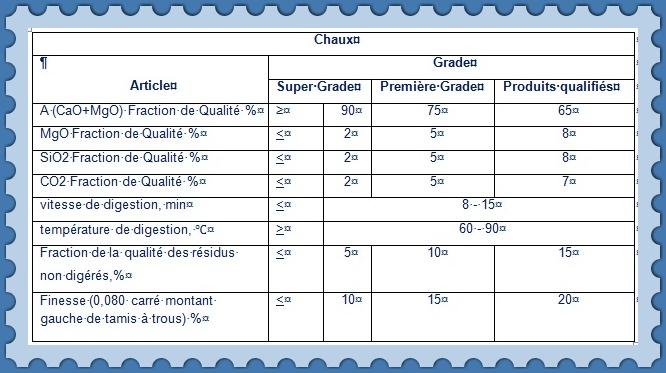
Gypse: C’est le régulateur moussant en AAC qui dissipe la chaux vive et reporte la densification de suspension.

Poudre et pâte d’aluminium: Ils doivent être moussant matériaux travaillant comme agent moussant faire des trous d’air pour former la structure poreuse.
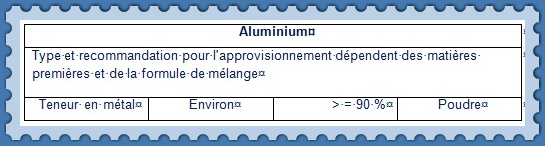
Caractéristiques physiques d’AAC bloc:
B04 grade: densité moyenne de 400 – 425 kg/m3, pression de 2.0 – 2.5 Mpa
B05 grade: densité moyenne de 500 – 525 kg/m3, pression de 2.5 – 3.5 Mpa
B06 grade: densité moyenne de 600 – 625 kg/m3, pression de 3.5 – 5 Mpa
Disposition de travailleurs
(Juste pour la référence et dépend de la situation locale)
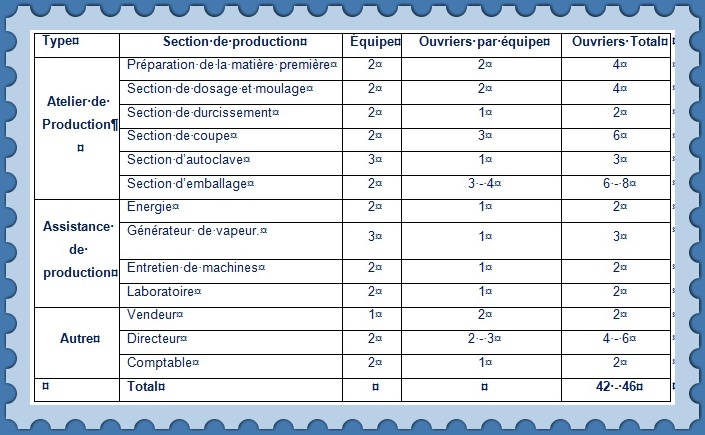
Dimension de bloc béton cellulaire
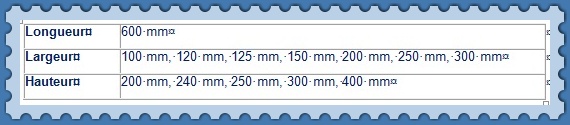
Stockage des matières premières
Sable, du ciment, de la chaux, du gypse, de la pâte d’aluminium doit être stocké séparément dans le parc de stockage de matières premières et les utiliser dans le besoin.
-
-
Silos de Stockage des matières premières.
-
-
Broyeur à sable
-
-
Silo de boue de sable avec agitateur et mesure de densité
Le sable siliceux sera transporter du Silos de stockage pour être broyé en fine boue de sable dispersée dans un broyeur à boulets humide, puis stocké dans le Silo de boue de sable avec agitateur et mesure de densité
Il est important de garder constamment ou continuellement la densité spécifiée et réglée soit manuellement, soit automatiquement.
Dosage et Mélangeage
-
-
Moulage
-
-
Mélangeur de matières
premières.
La boue de sable, les boues de retour, de la chaux, du ciment, du gypse, de l’agent aluminium et de l’eau sont dosés automatiquement conformément à la prescription de produit respective dans le mélangeur.
Moulage, Fermentation et Démoulage
-
-
Moulage
-
-
Fermentation
-
-
Démoulage
Moulage:
Le cycle de moulage sera contrôler chaque 5 minutes ou maximum 5,5 minutes
Nous utilisons le system Allemand de AAC-Concept
5 minutes x 167 moules = 835 minutes ≈ 14 heures ≤ 22 heures.
Pré-durcissement, fermentation:
Habituellement, le temps de Pré-durcissement est de 3 heures dans un cycle, nous pouvons avoir 7 cycles de pré-durcissement par jour (pendant 22 heures), de sorte que 167 moules ÷ 7 cycles = 24 moules par cycle.
Le minimum qu’on transport en salle de pré-durcissement est 24 moules par cycle, par ce que les moules doivent retourner au processus, après qu’ils sont nettoyés graissés et entretenus.
Donc nous ajoutons de 2 moules supplémentaires (un total de 26 moules) pour garantir la production.
Afin de garantir l’efficacité et le temps de pré-durcissement, la chambre de pré-durcissement est conçue en deux côtes de traversier chariot à deux lignes, afin de faire rentrer ou sortir chaque moule.
Une certaine quantité de la masse provenant de mélangeur sera versée dans un moule huilé constitué de deux parties et à fermeture extrêmement étanche. Dans ce moule, le gâteau de béton cellulaire fermente env. 2,5 heures dans une chambre de fermentation chauffée, afin de pouvoir durcir à des températures bien définies.
Le moule a été spécialement conçu en vue de l’opération de basculement qui est ensuite effectuée. Il se compose d’une structure sans torsion dotée de parois latérales coniques et pouvant être retirées par le haut. Cela permet de retirer le gâteau du moule en douceur et de façon impeccable. Le fond du moule et les parois se rejoignent toujours exactement, de sorte à former une unité parfaite.
Le retrait de moule du fond des formes, – appelé également décoffrage – ainsi que le transport ultérieur sont effectués au moyen d’une installation à portique. Le gâteau vert fait l’objet de très peu de manipulations – tout en douceur – de sorte que les dommages, comme des fissures ultérieures qui sont par ailleurs visible après l’autoclavage, ne se pose pas.